HERE’S WHY
There are people who “Sell” brake pads and those who make them… EBC does both and because we actually make all the brakes we sell, it stands to reason we know quite a lot about different friction materials. EBC has its own fully qualified R and D engineers, more than ten dynamometers, full chemistry, and test labs with shear test, density test, hardness testing, everything required to be a world-class brake pad manufacturer and have over 200 pad blends in our arsenal, the latest and best 6 of which forms today’s EBC range.
EBC sells both automotive and Motorcycle brakes but in this article, we will address only the automotive range we make.
The following article represents our opinion and findings over 40 years of making over 100 million sets of brake pads, quite a lot of experience. Our findings differ from a lot of verbiage that is on the market today and we hope you enjoy it’s reading.
Understanding the materials or systems that go into brake pads is an interesting starting point. Brake pads include resins to stick the pad elements/material together, fiber to bind the pads during manufacture, fillers to bulk out the pad, and then a collection of ingredients to enhance the pad friction levels and fade resistance. Abrasives and even lubricants are used in the design of a balanced pad and then noise reduction ingredients to dampen vibration and therefore noise.
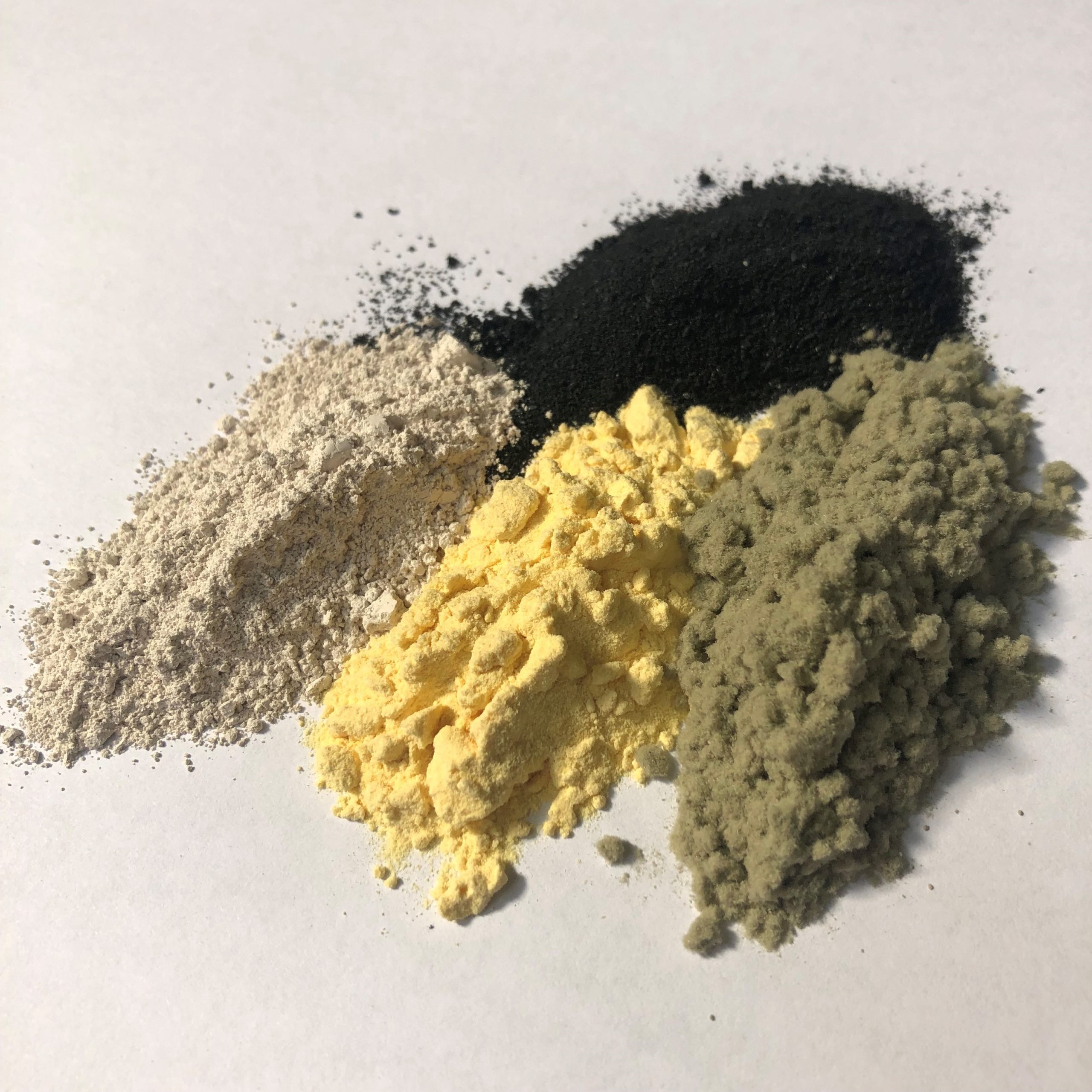
Basically, there are four different grades of brake pads on the world markets – 1) semi-metallics, 2) organics, 3) ceramics, and the newest of all types – 4) NAO Ceramic enhanced formulations.
- Semi – Metallics
The lowest cost materials to blend where steel fibers constitute half or more of the brake pad volume. These deliver a good brake effect but are often noisy and require good shim hardware to quieten them down. They are more aggressive in the way they deliver stopping power (and will wear rotors faster) and are also dustier. In tests done at EBC we found that 90% plus of the dust coming from semi-metallic brakes is iron or steel and it is almost certainly steel fibers from the pads or iron from the rotor (rotor abrasion) that is emitted. Dust in semi-metallic pads is also darker and can cause hot sparks that attach to wheels and can damage alloys and wheel lacquer and causes that nasty red rust powder you see on wheels as the pad nears the end of its life.
When the world switched away from asbestos many years ago, steel fiber was the go-to replacement as a binding fiber/filler. (EBC has never used asbestos by the way. ). Steel fiber was low-cost and did the job of producing the requisite “snowballing” effect in the pad mix to allow handling as the pad moves from a preformed state into the final baking process.
As mentioned above, steel fibers can constitute around 50% of the pad volume, far more than is actually needed in the manufacturing process but it’s a good and inexpensive filler so the job was done!
As far as we have seen almost all OEM factory pads are semi-metallics.
A major negative with semi-metallics is the ability to bond what is, in effect, steel to steel with even modern adhesives and that’s why for ALL of its brake pads EBC uses the NRS hook retainer system.
- Organics or NAO pads (Non-asbestos organics)
These contain little or no steel fibers, typical 4-7% by pad volume, this allows more room within the pad mix to add in some tasty ingredients that enhance the pad performance. For this reason, organics tend to be more expensive to make than semi-metallic pads.
To make up for the low percentage ( or zero percentage ) of steel fibre in the pad mix other man made fibers are used which vary and include proprietary products such as Dupont Kevlar, Lapinus, Rockwool or Twaron.
EBC brakes use all of the above in different pad blends.
EBC Greenstuff, Yellowstuff, Bluestuff are all NAO pads and you can read more about these by clicking on their name to the left.
- Ceramics
It is amusing to see some writers liken Ceramic pads to materials used in coffee mugs or plates, not a very exciting thought to be using a coffee mug to stop a vehicle. However, in particle form, the correct particle size particles of Ceramic materials can be a useful additive to a decent pad blend. However, the percentages are very small. Excess content would ruin pad performance.
Ceramic fibers are also not a path EBC has ever gone down for health reasons in manufacture.
- NAO Ceramic enhanced
Probably the more correct description for what the market sees as a ceramic pad is an organic base pad, which we call a Para-Aramid,with a small percentage of Ceramic granules and lots of other fancy ingredients to create a balanced pad.
NAO ceramics are quieter and less dusty and generally, we find the addition of “some” ceramic in granule form can make a pad last longer. Basically, this is something EBC has been doing for years using not only ceramic granules but things like Barites,Vermiculite, and other similar mined ores.
Examples of EBC NAO Ceramic blends are EBC Redstuff pads for cars and the new EBC ED extra duty plus red coded range for Jeep ® Light truck and SUV 4 x 4
- The Environment
In line with upcoming automotive brake pad legislation EBC has eliminated copper from all of its automotive range and has, years ago been a world leader in eliminating nasty things like Antimony from pad mixes. There is also no lead, mercury, nickel, or any other known carcinogens in EBC products, a range of truly ECO-friendly brake pad materials